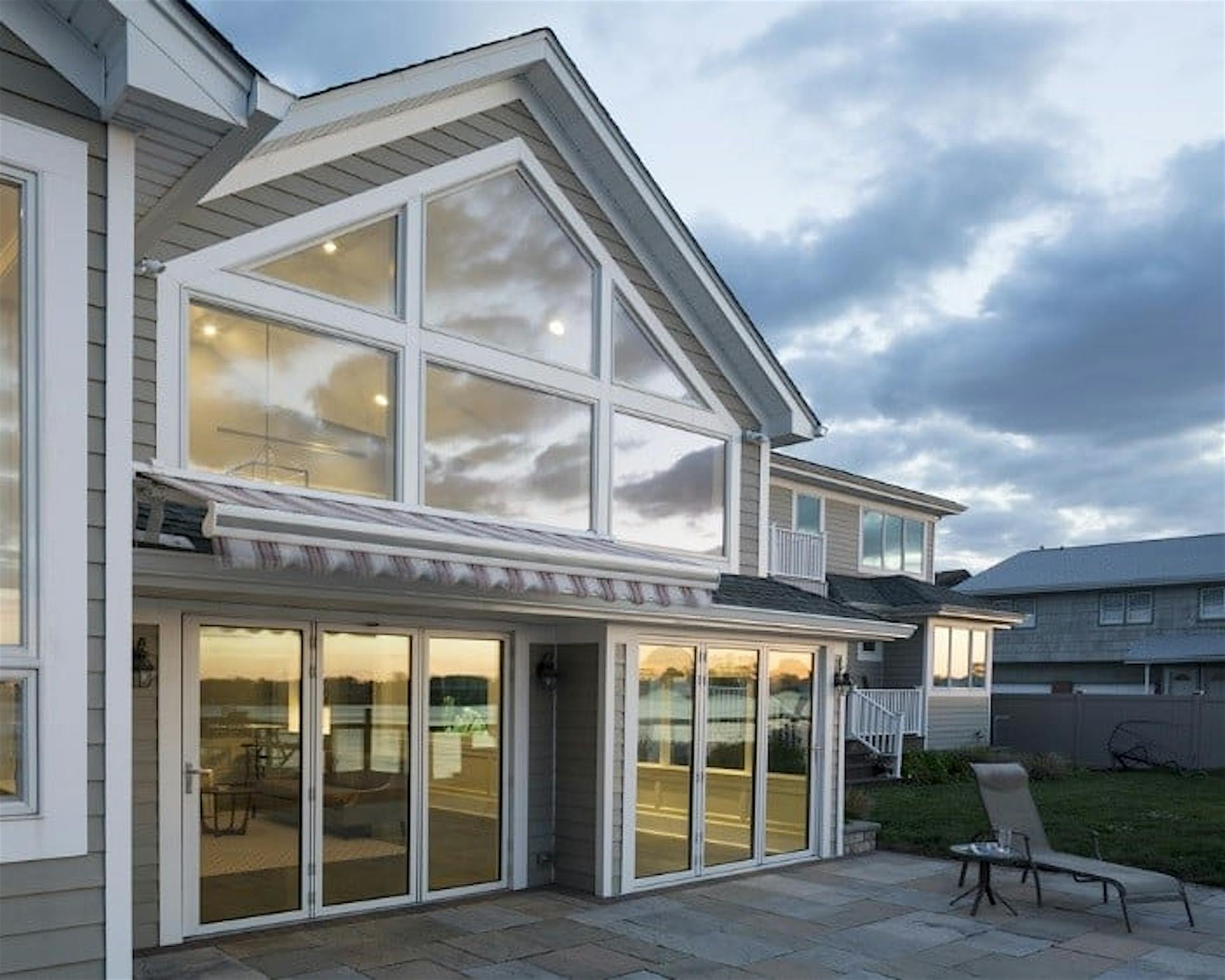
When Hurricane Irma hit South Florida in September 2017, residents and business owners braced themselves for the worst. Packing 130-mph winds when it made landfall in the Florida Keys, Irma caused widespread damage on both the Gulf Coast and in the Miami area where fierce winds toppled construction cranes and pushed water through window seals and roof joints at Miami International Airport.
Even though Miami-Dade certification requires glass walls to have sufficient impact resistance and cyclic wind pressure load ratings, we still saw Irma, Maria and Harvey wreak massive destruction upon the buildings left in their wake. As opening glass wall systems become a staple of architectural design, we need to recognize that Miami-Dade compliance ought to be used as a jumping off point, rather than a pinnacle of achievement.
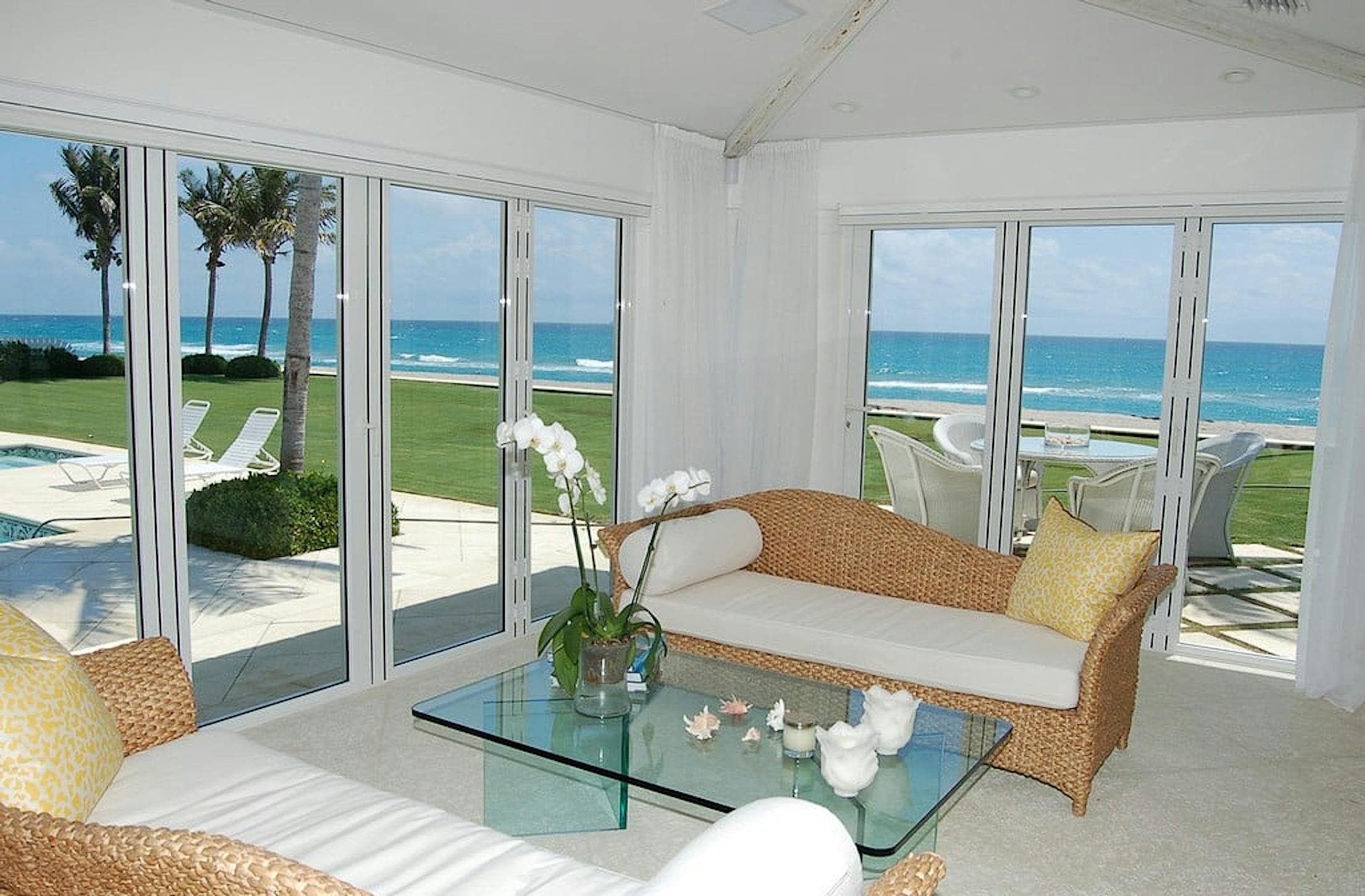
Due to the rising sea-levels caused by climate change, storms are increasing in frequency and ferocity with each passing year. Doing the minimum required is not going to be enough to ensure that our constructions can withstand superstorms. For safety, security, and real endurance that we can rely on, we have to go further.
For architects and builders rebuilding in hurricane zones, we have made a list of opening glass wall features vital to ensuring that a glass wall system can perform above and beyond Miami-Dade.
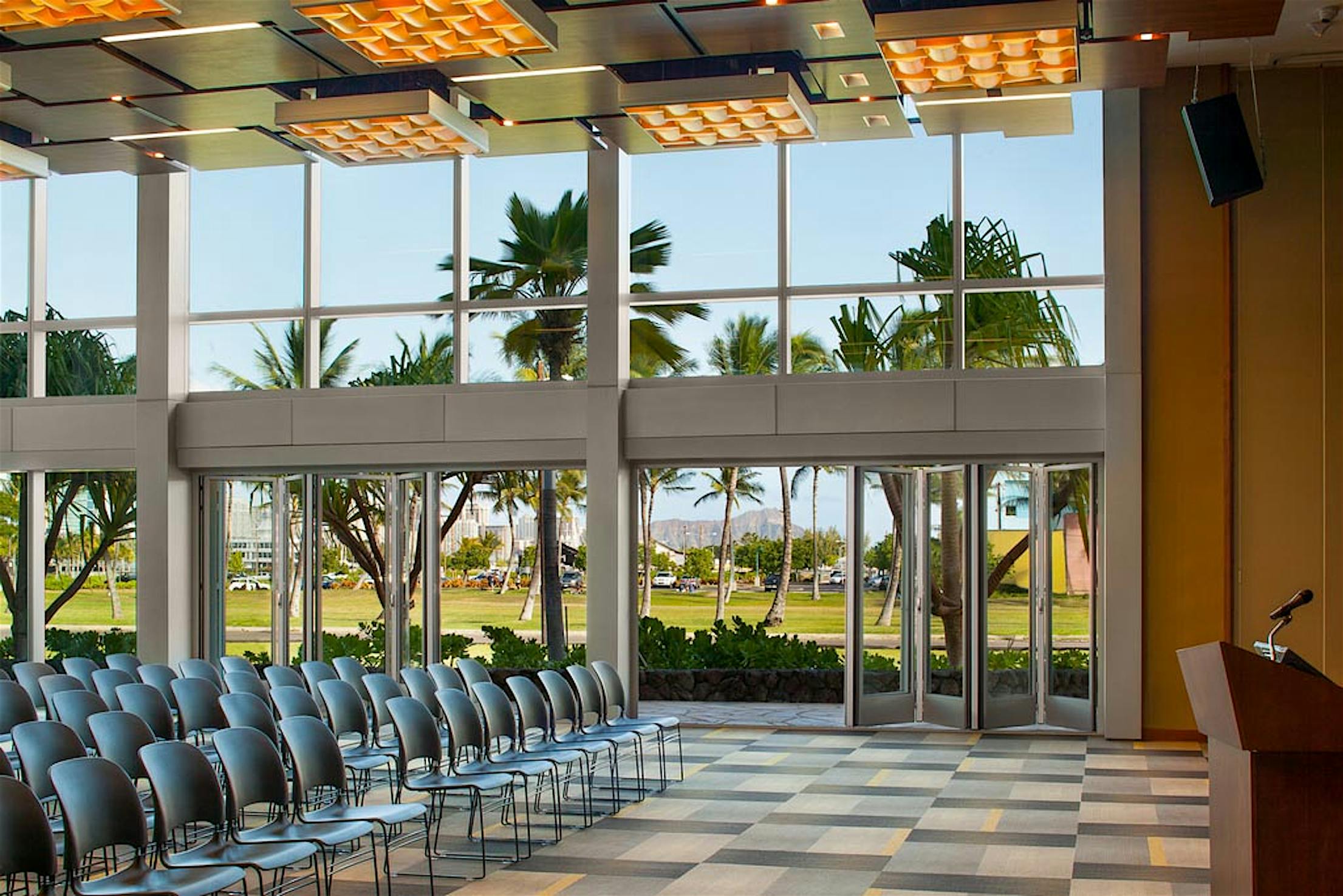
6 Key Features of Hurricane Resistant Opening Glass Walls
1. Reinforced structural posts: Look for a folding glass wall system with reinforced vertical posts (or astragals) that run alongside each panel for added performance. These posts provide incredible strength that allows the system to withstand high winds and water penetration. This design ensures that the panels pivot on and are hinged to either side of the vertical post, as opposed to pivoting on rollers with ball bearings. The posts themselves should have stainless steel wheels that run along a stainless steel track, sans pivoting.
2. A floor supported system: Many glass wall systems are top-hung and use the floor rail solely to guide the panel’s path. Heavy, moveable panels require an incredibly strong header to avoid making the glass walls susceptible to high winds. Floor supported systems, on the other hand, use gravity to their advantage by letting the floor support the weight. This additional reinforcement instability further enables the glass wall system to withstand hurricane force winds.
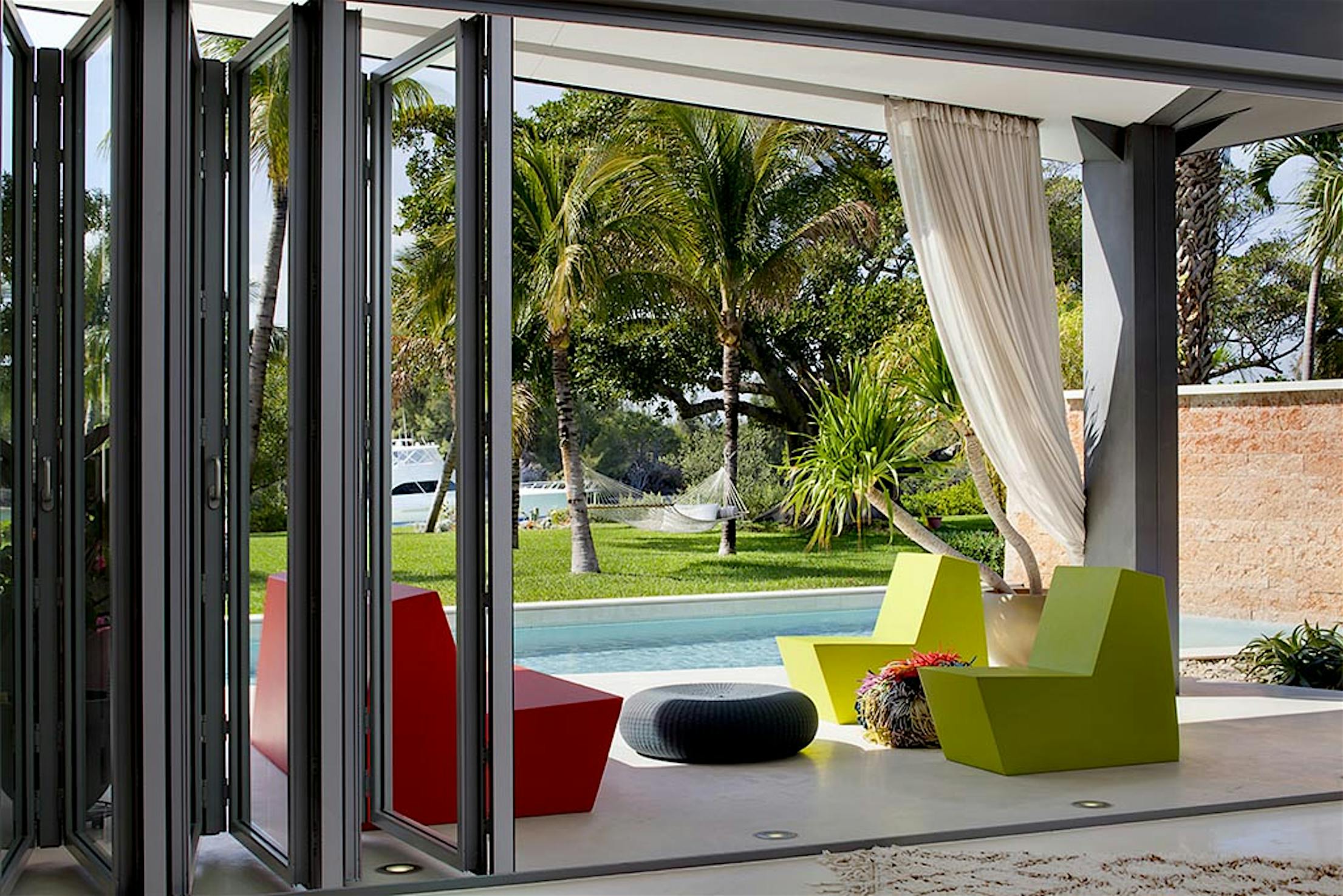
3. Raised sills: Extreme weather means that water, mud, and other particulates will be pressed against the glass, seeping in through the floor tracks, ruining both wood and carpet. A high-performance raised sill is the most weather-resistant sill available. It prevents both static and dynamic water penetration and provides higher pressure ratings against heavy wind loads. The result: even without an overhang to shield it from the elements, these opening glass walls can face even the strongest winds head-on.
4. Corrosion resistance: Not only do you need extruded aluminum frames and panel profiles (an absolute must when it comes to protecting against saltwater-filled air), but check to ensure that the rollers and hinges are made of stainless steel. When salty wind and rain are beating down upon a system, the parts can quickly rust and corrode, weakening the system’s ability to perform against future storms.
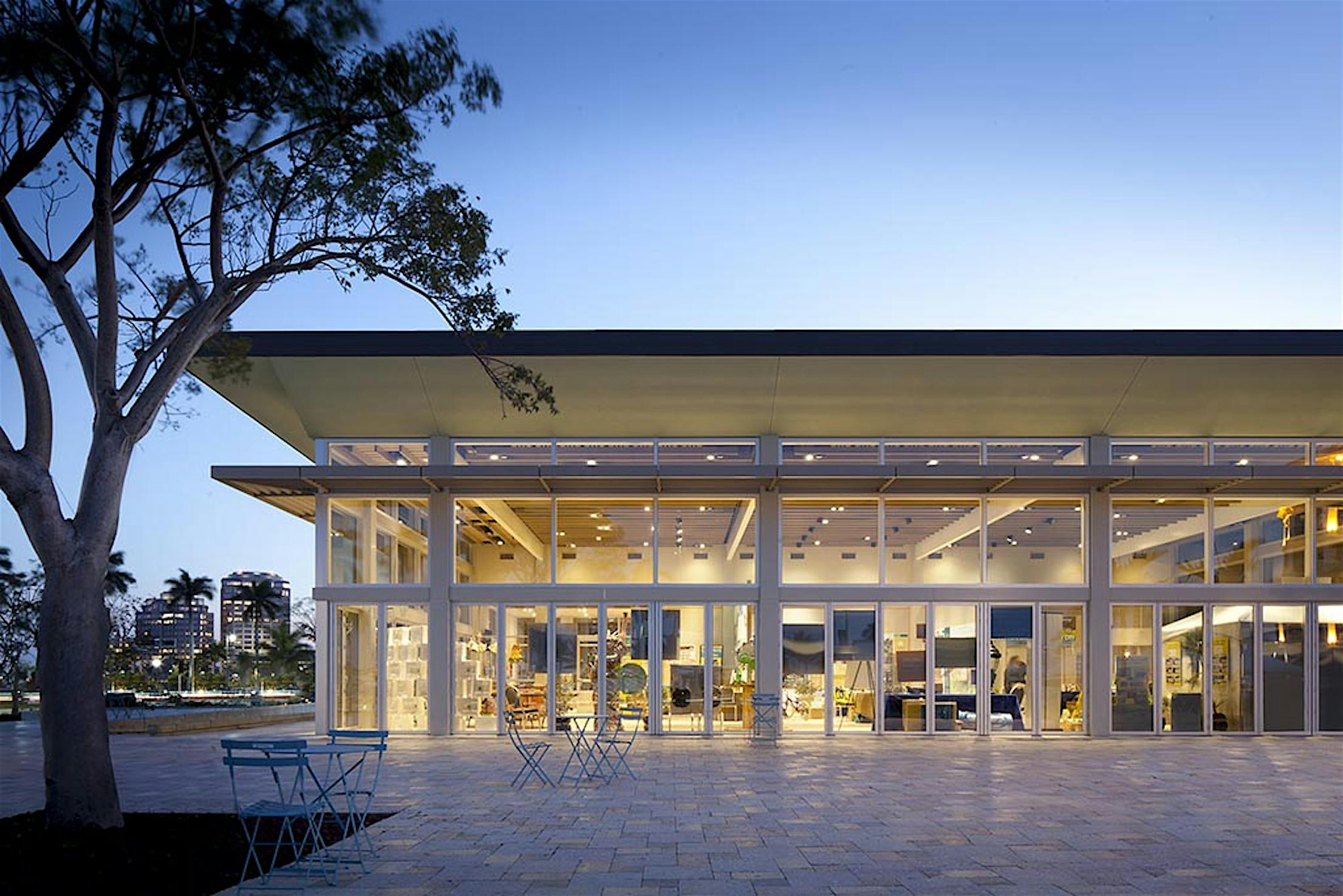
5. Multipoint locking: Vandalism and burglary are a real issue once residents have been evacuated, leaving their homes and businesses unprotected until cleanup efforts are underway. Looters will usually look for easy points of entry, often breaking in through sliding or folding glass walls. A latch and a deadbolt is not enough to secure an opening glass wall.
A multipoint locking system that includes top and bottom polyamide capped locking rods that can lock each glass panel into the upper and lower frame individually is paramount. The multipoint locking will not only secure the opening against unlawful entry, but also adds yet another layer to its ability to withstand strong winds and water intrusion.
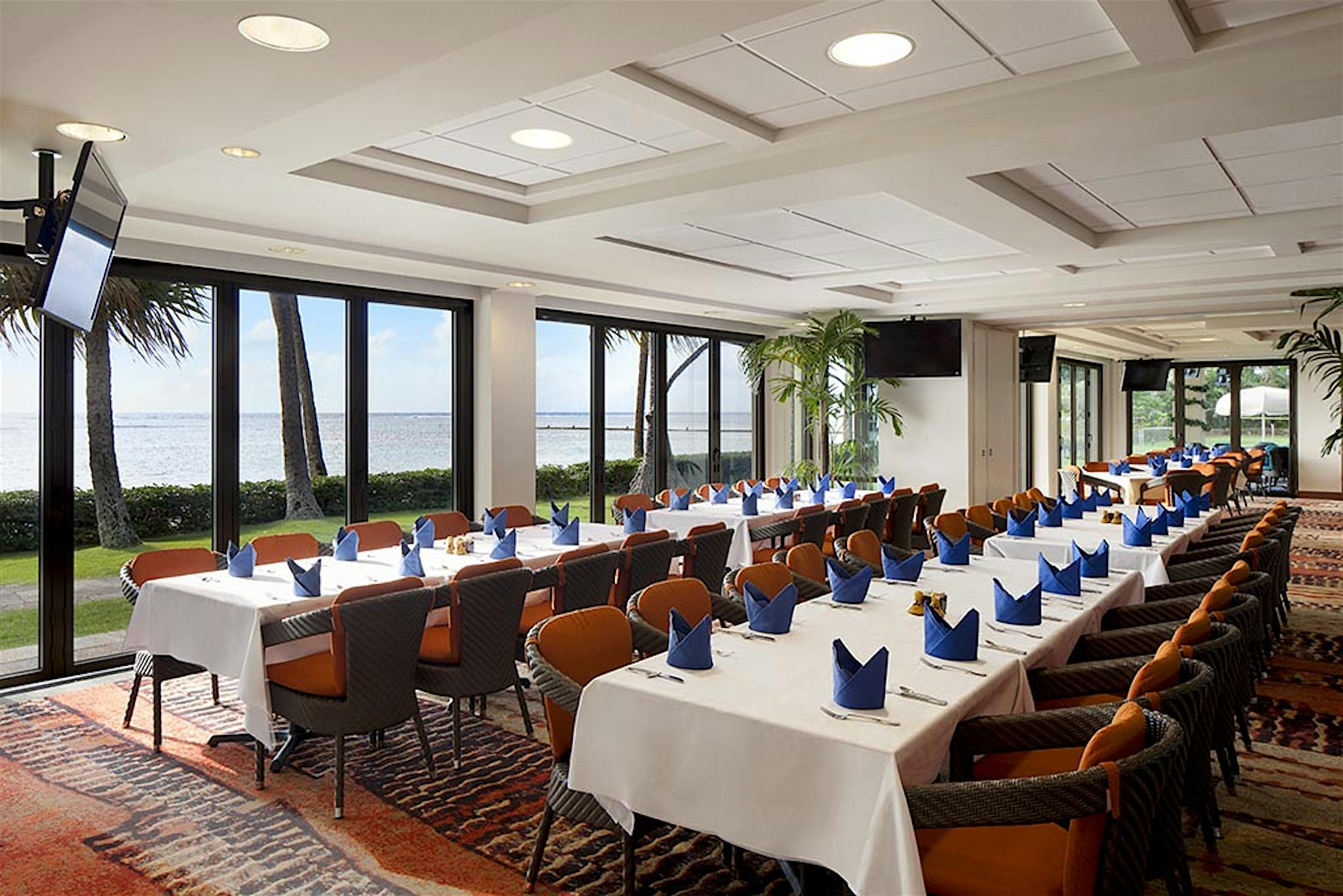
6. Additional certifications: Ratings for Miami-Dade, American National Standards Institute (ANSI), and American Society for Testing and Materials (ASTM) are just the baseline. Any glass wall system being installed in hurricane country worth it's salt ought to have additional climate performance and durability certifications. Look for high air, water, structural, and forced entry ratings from the American Architectural Manufacturers Association (AAMA); as well as National Fenestration Rating Council (NFRC) certifications for air leakage and condensation resistance.
This past hurricane season showed us that Miami-Dade County certification is just the tip of the iceberg where ensuring safety, security, and structural performance is concerned. During this rebuilding process and moving forward, architects and builders should look for glass wall systems like our SL73, that go well beyond the Miami-Dade standards toward peak performance.
Questions about our SL73 and hurricane-resistant opening glass walls? Connect immediately with a NanaWall expert.